Czochralského metoda
Jako Czochralského metoda (anglicky Czochralski process) se označuje jedna z technologií růstu syntetických monokrystalů. Výsledným produktem je monokrystal o přesně definované krystalografické orientaci s velmi pravidelnou krystalickou mřížkou. Nejčastěji se jedná o monokrystaly křemíku, germania nebo arsenidu gallitého. Czochralského metoda stojí téměř na počátku výroby polovodičových integrovaných obvodů, se kterými se lze setkat v oblastech výpočetní techniky, mobilních telefonů a u mnoha dalších elektronických zařízení. Základní princip výroby křemíkového monokrystalu Czochralského metodou spočívá ve vzniku taveniny vysoce čistého polykrystalického křemíku a v následném tažení monokrystalu z této taveniny pomocí zárodku o přesně stanovené krystalografické orientaci v Czochralského tažičce. Mezi nejdůležitější požadavky výroby patří bezdislokační růst monokrystalů, kterého lze docílit vysokou čistotou vstupních surovin a prostředí.
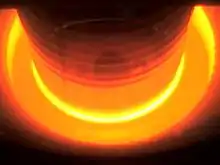
Historie
Technologie tažení monokrystalu touto metodou byla objevena v roce 1916 polským chemikem Janem Czochralskim, po němž je pojmenována. Czochralski pracoval v laboratořích AEG a při experimentech omylem ponořil pero do kelímku s roztaveným kovem. Po vyjmutí pera zjistil na jeho konci monokrystalický charakter taveniny.[1][2] Ve 40. letech pracovali na zdokonalení metody v Bellových laboratořích výzkumní pracovníci Gordon Kidd Teal a J. B. Little. V roce 1959 bylo do výroby zavedeno Dashovo zúžení. Od roku 1985 se stala Czochralského metoda hlavní technologií výroby monokrystalického křemíku a v roce 2004 se Czochralského metodou růstu monokrystalu vyrábělo přes 95 % světové produkce.[1]
Tažička
.JPG.webp)
Vlastní růst objemového monokrystalu křemíku probíhá v zařízení zvaném tažička (anglicky puller). Tažička se skládá ze dvou komor umístěných nad sebou a oddělených vakuově těsnou oddělovací klapkou.[1]
Horní komora je podle provedení vybavena lankem nebo hřídelí, které slouží jako držák zárodku nebo legovací ampule. Nad horní komorou je také umístěn celý mechanismus, který zajišťuje rotační pohyb lanka nebo hřídele. Horní komora pak slouží především k uchování již vytaženého krystalu, dále je používána při vyjímání vyrobeného krystalu nebo zde v průběhu tavby probíhá výměna zárodku monokrystalu za legovací ampuli nebo naopak.
Dolní komora tažičky je vyrobena z dvouvrstvé nerezové oceli a po celou dobu tavby je neustále chlazena vodou.[1] V této komoře se nachází celá topná zóna i křemenný kelímek s taveninou. Také zde probíhá vlastní tažení monokrystalu.
Topná zóna nebo topný uzel (hot zone) je složen z řady grafitových dílů. Základem topné zóny je topidlo, které se průchodem elektrického proudu zahřívá až na teploty kolem 2000 °C. Topidlo je umístěno na dvou nebo čtyřech patkách. Dvě patky jsou vždy živé, tedy napájené elektrickým proudem, další dvě patky pak slouží především k podepření topidla.[1]
Další součástí dolní komory jsou stínící prvky, jenž slouží k odrážení tepla dovnitř komory a zamezují tak tepelným ztrátám.[3] V dolní komoře se nachází hřídel umožňující rotační i svislý pohyb, na níž je umístěn grafitový kelímek.[1] Uvnitř grafitového kelímku se nachází křemenný kelímek. Dolní komora je vybavena potrubím pro odtah argonu a nečistot, dále také několika průzory, pyrometrem pro snímání teploty, kamerou pro snímání průměru krystalu a případně také katetometrem.
Obě komory disponují přívody argonu. Vakuově těsná oddělovací klapka slouží k oddělení jednotlivých komor. Vzhledem k tomu, že celý proces tažení monokrystalu Czochralského metodou probíhá v inertní atmosféře argonu (v obou komorách je podtlak),[4] zajišťuje tato klapka možnost oddělit komory v průběhu tavby a horní komoru napustit na běžný atmosférický tlak.[3] Toho se využívá například při legování, kdy dochází k výměně legovací ampule za zárodek již v průběhu tavby.
Polykrystalický křemík
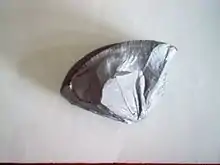
Jednou ze základních vstupních surovin pro výrobu monokrystalu křemíku Czochralského metodou je vysoce čistý polykrystalický křemík. Běžný polykrystalický křemík se získává z přírodního křemene procesem zonální rafinace v elektrické obloukové peci. Takto získaný hutní křemík dosahuje čistoty přibližně 97–99 %.[1] Pro výrobu diskrétních elektronických součástek je však vyžadována čistota vstupního materiálu na úrovni ppb (parts per billion) a vyšší. Takto vysoké čistoty materiálu lze nejčastěji docílit využitím Siemensova postupu. Při tomto chemickém postupu dochází ve fluidním reaktoru k reakci chlorovodíku s hutním polykrystalickým křemíkem za vzniku těkavého trichlorsilanu.[1] Následným vedením trichlorsilanu přes vrstvu čistého křemíku dochází k jeho rozkladu a poté k řízené krystalizaci na zárodečném jádře. Čistota takto získaného polykrystalického křemíku může dosahovat až hodnot ppt (parts per trillion).[1]
Výroba monokrystalu
Příprava vsádky
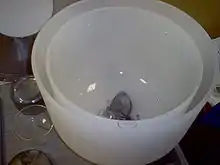
Před vlastním započetím tavby je třeba připravit vsádku polykrystalického křemíku. Příprava vsádky probíhá systematickým ukládáním polykrystalického křemíku do křemenného kelímku, a to takovým způsobem, aby se při ukládání minimalizoval styk styčných ploch kusů polykrystalického křemíku a stěn křemenného kelímku. Při přípravě vsádky se dbá také na to, aby se na dně kelímku nacházely menší kusy křemíku. Větší kusy, uložené nahoře, se následně při tavení propadají dolů.[1] Obvyklá hmotnost jednotlivých vsádek se podle požadovaného typu krystalu pohybuje od 5 až do 400 kilogramů.[1] Samotný křemenný kelímek lze použít pouze na jedinou tavbu. Při tavbě dochází vlivem vysoké teploty k jeho deformaci nebo úplnému rozbití.[4] Do některých vsádek se také přidávají podle požadovaných vlastností krystalu různé typy legur.
Tavení
Připravená vsádka se uloží do vícedílného grafitového kelímku v Czochralského tažičce. Po spuštění tavby dochází nejprve k vyčerpání vzduchu, při nedokonalém vyčerpání může být celá tažička opakovaně proplachována argonem. Jestliže jsou podmínky uvnitř tažičky vyhovující, dojde ke spuštění tavení vsádky. Při tavení se hodnota příkonu pohybuje na hodnotách okolo 100 kW u 400mm topné zóny.[1] Tavení vsádky probíhá řádově v hodinách a může při něm dojít k přitavení kusů polykrystalického křemíku na stěny křemenného kelímku. Nedokonalé roztavení vsádky lze považovat za nežádoucí, neboť může ovlivnit výsledné parametry krystalu.[1] Při tavení dosahuje teplota uvnitř tažičky až 1500 °C. U roztavené vsádky poté probíhá proces stabilizace vsádky, jehož cílem je ustálit proudění a teplotu taveniny.[1]
Legování
Legování je proces, při kterém je do taveniny přidáván určitý typ dopantu (legura). Druh a množství legury ovlivňuje některé požadované parametry krystalu, například jeho měrný odpor.[1] Konkrétní typ dopantu ovlivňuje výsledný druh monokrystalu, a to podle toho, zda je požadován polovodič typu P nebo polovodič typu N.[2] Legování probíhá dvěma způsoby. Jestliže má dopant vyšší sublimační teplotu, než je teplota tavení vsádky, a nehrozí tedy jeho odpaření ještě před roztavením vsádky, vkládá se taková legura přímo do vsádky. To se týká například legování borem. Má-li dopant nižší sublimační teplotu, hrozilo by při vložení do vsádky jeho předčasné odpaření. V takových případech se legování provádí pomocí legovacích ampulí. Legovací ampule jsou vyrobeny z vysoce čistého křemenného skla.[1] Přesně stanovené množství a typ legury se vloží do legovací ampule a po úplném roztavení vsádky se tato ampule spustí do taveniny. Poté dochází k odpařování legury přímo do taveniny, která ji pohlcuje. Legování pomocí legovací ampule se využívá při krystalech s dopanty fosforu, arsenu nebo antimonu (v případě antimonu se dopant neodpařuje, ale taví se a skape do taveniny).[1] Podle množství legury pak existují slabě nebo silně legované krystaly.
Tažení
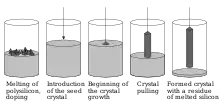
Po roztavení vsádky, legování taveniny a stabilizačním procesu dojde k samotnému procesu tažení monokrystalu. Základem pro tažení krystalu je monokrystalický zárodek (seed) o přesně stanovené krystalografické orientaci.[5] Zárodek má tvar válce o průměru přibližně 10 mm. Tento zárodek je spuštěn na lanku nebo hřídeli do taveniny, kde dojde na fázovém rozhraní mezi taveninou a zárodkem k teplotnímu šoku. Ponořená část zárodku se odtaví a zárodek na fázovém rozhraní se protaví. Protavení zárodku lze pozorovat přes průzor a je patrné při vzniku růstových bodů na fázovém rozhraní.[1] Následným zvýšením rychlosti tažení zárodku dojde k postupnému zúžení zárodku až na hodnotu přibližně 5 mm. Takto vzniklé Dashovo zúžení se táhne v délce asi 5 cm a jeho cílem je zabránit dislokačnímu růstu monokrystalu.[1] Po správném růstu zárodku dojde ke snížení rychlosti tažení a tím k rozšiřování zárodku, který přejde v růst hlavy (crown growth). Po růstu hlavy o stanoveném průměru následuje tažení zarovnání (shoulder growth) a poté nejdůležitější tažení samotného těla krystalu (body growth). Po vytažení části monokrystalu o přesně stanovené hmotnosti následuje růst špice (tail growth), kdy dochází k opětovnému zúžení krystalu. Při oddělení špice od taveniny na konci tavby dojde k opětovnému teplotnímu šoku a ke vzniku dislokací, které se šíří zpětně do špice. Z vytaženého monokrystalu je pak využitelná pouze část těla krystalu, hlava i špice monokrystalu jsou považovány za odpad.[1] Z původní vsádky je při úspěšném růstu krystalu vytaženo přibližně 90 % materiálu, zbytek zůstane na dně křemenného kelímku a není již dále využitelný.[1] Základním požadavkem pro úspěšný růst monokrystalu Czochralského metodou je eliminovat možnost vzniku dislokací v jakékoliv fázi tažení monokrystalu.
Při tažení monokrystalu se využívá protisměrné rotace kelímku a krystalu,[5] přičemž rychlost otáčení krystalu je výrazně vyšší než rychlost rotace kelímku.[4] Tato protisměrná rotace zajišťuje správné proudění taveniny a vhodné podmínky pro růst krystalu. Pro udržení konstantní pozice fázového rozhraní pak slouží parametr RATIO. Tento parametr zajišťuje při úbytku taveniny v kelímku postupný zdvih kelímku a je charakterizován jako poměr rychlosti zdvihu kelímku vůči rychlosti zdvihu krystalu (CL/SL RATIO, crucible lift/seed lift RATIO).[1][4]
U různých typů monokrystalů se může podle požadavků lišit krystalografická orientace. Nejčastěji je možné setkat se s orientacemi 100 a 111. Základní orientace je při tažení dána již vloženým zárodkem. Orientace 100 se při růstu monokrystalu vyznačuje vznikem čtyř růstových bodů a následně čtyř švů na těle krystalu. Orientace 111 je charakteristická šesti růstovými body a vznikem tří fazet (ploch) na těle krystalu.[1]
Podmínky pro růst monokrystalu
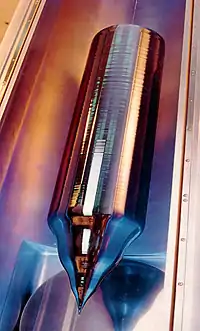
Jednou ze základních podmínek správného růstu monokrystalů Czochralského metodou je vysoká čistota vstupních surovin a také tažičky. Veškerá manipulace se vsádkou, včetně její přípravy, probíhá v čistých prostorách třídy minimálně 100 000.[1] V klimatizovaných čistých prostorech je vytvořen mírný přetlak, který brání vniknutí nežádoucích částic z nečistých do čistých prostor. Proškolená obsluha zařízení pracuje ve speciálních kombinézách a většinu operací, především jakoukoliv manipulaci s čistým polykrystalickým křemíkem nebo se zárodkem, provádí ve vinylových rukavicích.[1] Obsluha využívá při práci bezprašné materiály a dodržuje pravidla a předpisy pro práci v čistých prostorech.
Pro růst monokrystalu uvnitř tažičky je dále nezbytné zajistit trvalý průtok argonu nebo jiného inertního plynu, který brání vzniku nečistot uvnitř zařízení a zamezuje napařování oxidů křemíku na stěny křemenného kelímku. Neméně důležitou součástí růstu monokrystalů je zajištění trvalého příkonu zařízení a udržování trvalého průtoku chladicí vody.
Velikost monokrystalů
Výsledná velikost monokrystalů je dána hmotností vsádky a velikostí topné zóny, z níž je krystal tažen. Nejčastější požadované průměry křemíkových leštěných desek (waferů) jsou 200 a 300 mm. Existují i menší průměry krystalů, s pokročilými technologiemi však dochází k růstu větších krystalů. Připravuje se technologie, která v roce 2018 umožní produkovat desky o průměru 450 mm.[6] Délka krystalu se pohybuje okolo jednoho nebo dvou metrů. Hmotnost krystalu činí řádově desítky až stovky kilogramů.[7] Výsledný křemíkový monokrystal se po vytažení z tažičky po provedení nezbytných testů rozřeže na jednotlivé desky, poté dochází k lapování a leštění waferů.
Galerie
- Monokrystalický zárodek
- Křemenný kelímek se zbytkem taveniny po tavbě je považován za odpad
- Monokrystal s hlavou, tělem a špicí
Odkazy
Reference
- Technologie růstu monokrystalů křemíku Czochralskiho metodou [PDF]. Československá společnost pro růst krystalů, 2004 [cit. 2015-04-08]. Dostupné v archivu.
- Czochralski process [online]. articleworld.org [cit. 2015-05-18]. Dostupné online. (anglicky)
- PÁLENÍČEK, Michal. Detekce a studium krystalových defektů v Si deskách pro elektroniku [PDF]. Vysoké učení technické v Brně, 2011 [cit. 2015-04-08]. Dostupné online.
- Kde se bere monokrystalický křemík? Tažení monokrystalů křemíku Czochralského metodou [online]. Materiálová věda [cit. 2015-04-08]. Dostupné online.
- ŠAVEL, Josef. Elektrotechnologie. Praha: BEN - technická literatura, 2005. 314 s. ISBN 978-80-7300-190-2. S. 65.
- MANNERS, David. Doubts over 450mm and EUV [online]. Electronics Weekly, 2013-12-30 [cit. 2015-05-18]. Dostupné online. (anglicky)
- ŠULC, Tomáš. Od písku k procesoru — výroba křemíkového waferu [online]. PC tuning, 2012-06-22 [cit. 2015-05-18]. Dostupné online.
Literatura
Související články
Externí odkazy
Obrázky, zvuky či videa k tématu Czochralského metoda na Wikimedia Commons